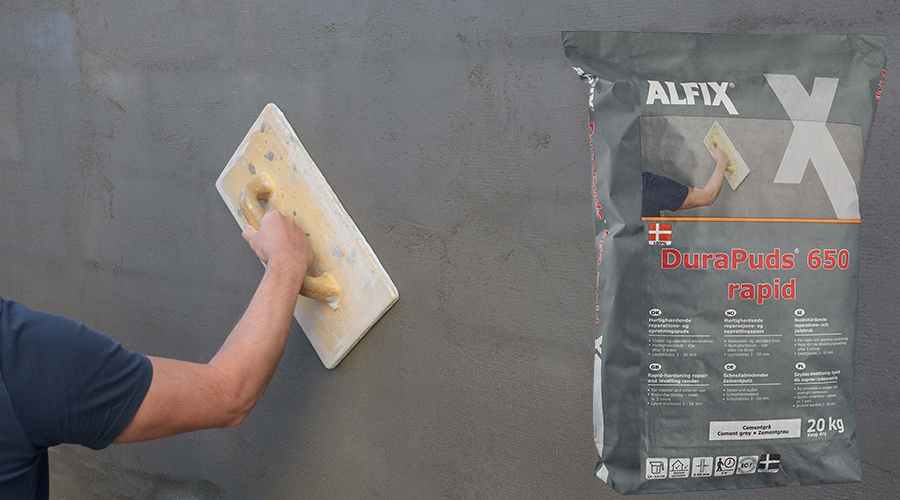
Alfix streamlines work on construction sites with rapid-hardening render
To meet increasing demand for materials and solutions that streamline workflow at the construction site, Alfix is now launching DuraPuds 650 rapid. This rapid-hardening repair and levelling render sets in just three to four hours and can therefore save the mason a lot of time – which is vital in today’s construction industry.
Alfix had very specific parameters in mind when developing their first quick-setting render – the first to be added to its product range.
“The need for investment in construction efficiency is ever-growing. Materials, solutions, methods and advice on and for construction efficiency have never been more in demand and relevant. That’s the backdrop for Alfix’s decision to bring out its first-ever quick-setting plaster. From the mason’s perspective, they want to see the plaster beginning to bond an hour into the setting process. The product we have created is very efficient, but also easy to work with and gives the mason the flexibility they need in their daily working lives,” says Kim Mathiasen, Innovation Manager at Alfix.
Masons factored in
Alfix DuraPuds 650 rapid has been developed specifically with repairs to masonry, both internal and external, in mind. It was felt that the need was greatest in this area.
“We consulted with those involved on-site, and involved them from the very start. We obtained feedback to make sure that the products would have the right properties and qualities,” Mathiasen tells us, continuing:
“The masons were really enthusiastic about the product as a substitute for the cement mortar, which they tend to mix themselves on-site. The speed of it is the most important factor, as it can put them a day ahead in their work. We also received positive feedback about the product’s strong adhesive properties, and the fact that it has the same hardening time regardless of whether you use 10, 25 or 50 mm of render.
The render is also shrinkage-compensated, which reduces the likelihood of tearing, scratches and cracking,
regardless of the thickness of the layer.
“Despite the emphasis on efficiency with our new render, it doesn’t mean we have compromised - it still has the strong technical properties that all Alfix products have,” the Alfix Innovation Manager confirms.
Efficiency, quality and technique
The quick-setting plaster is perfect for jobs such as repairing walls and embedding cables. Open to diffusion, the flexible plaster can be adjusted easily by the contractor. Its smooth texture makes use of a mortarboard easy. The result of this is a nicely sealed surface that is easy to work with.
“In terms of its application, Alfix DuraPuds 650 rapid will seem familiar to masons; the difference is that, by avoiding having to stand there mixing sand and cement at the construction site, the job will be more efficient, higher quality and improve technique,” Mathiasen explains.
As Alfix DuraPuds 650 rapid sets in just three to five hours, saving the mason a lot of time, Alfix believes that the product will soon become a permanent resident in the mason’s van for use on unforeseen repair and levelling jobs.
“The render is different from other similar products and fills a gap on the market. Our competitors have gone in a different direction and are focusing on optimising trowel technique. We, however, have chosen to focus more on the rendering technique, as we believe this is more beneficial on larger surfaces,” the Innovation Manager finishes.
The first pallets of Alfix DuraPuds 650 rapid have already been produced at the factory in Kolding. As such, the product is ready to take its place at construction sites all around Scandinavia.